Equipment used: 4 1/2 inch bench vise, 5 inch C Clamp, 1 3/16 Deep well and Regular 1/2 in dr socket, 1/2 inch deep well 1/4 in socket, 1 1/8 deep well 1/2 in dr socket.
As mentioned, soaked everything for a night or two with PB Blaster and WD 40.
1. Start pressing out metal sleeve with the 1/2 in deep well 1/4 drive socket, using bench vise to press socket and sleeve into 1 3/16 reg socket (with a deeper throated vise, one could go right to the 1 3/16 deep well):
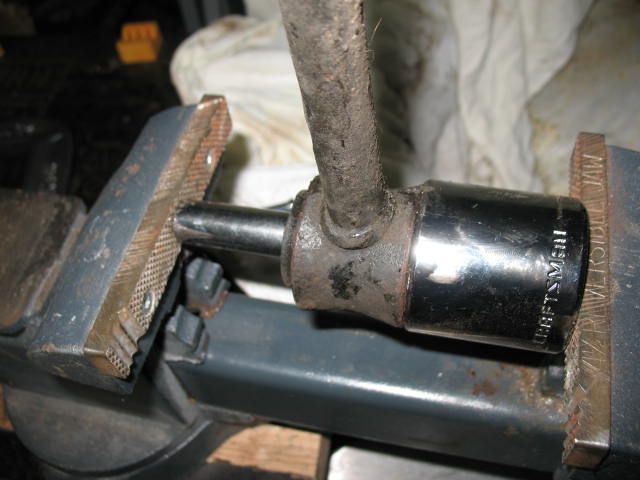
2. Finish pressing out sleeve with 1/2 in deep well, pressing sleeve into 1 3/16 deep well. 1 3/16 socket seems to keep the rubber bushing in place, allowing the sleeve to break adhesion and slide.
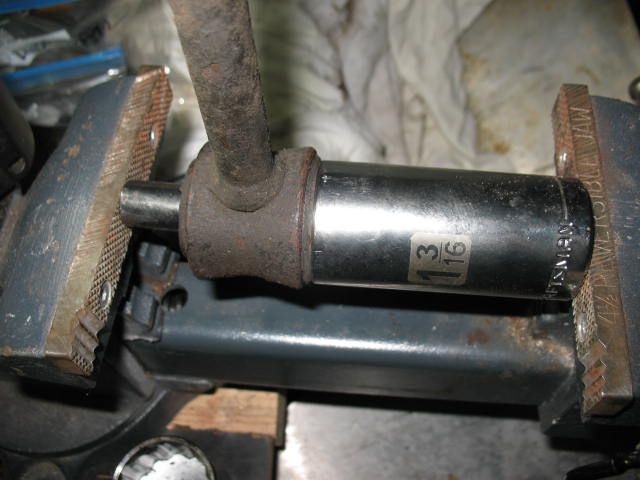
3. Clamp C Clamp into vise, and use C Clamp to press rubber bushing out into 1 3/16 regular socket. One learning point for me: rubber wants to ooze, so I learned to be patient, and apply additional screw pressure every other minute or so. Eventually the bushing softly pops out, and can be removed by hand after taking it out of the C Clamp.
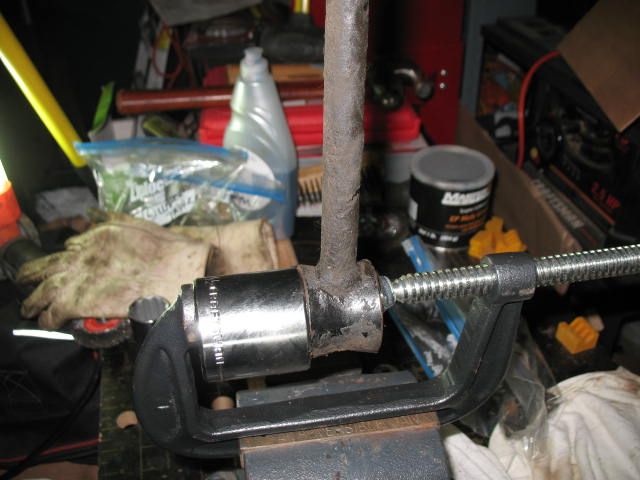
4. For stubborn ones, I added a 1 inch 1/2 dr socket to the pushing side, and used the bench vise.
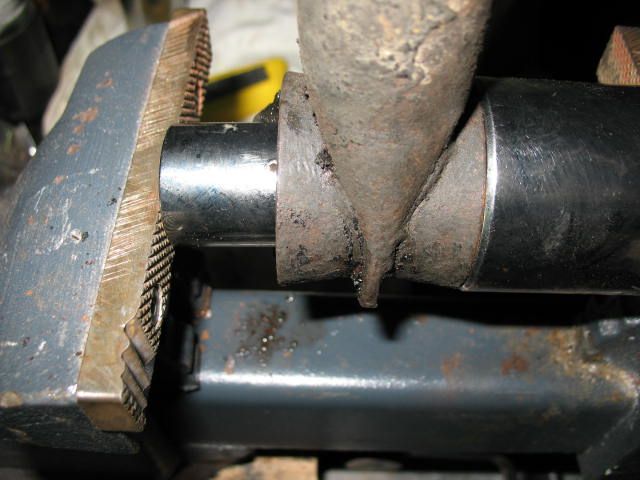
Got all but one out this way. I'll post some re-install pix once I get the trailing arms brushed, primed, and painted. Hope this helps !
Neil